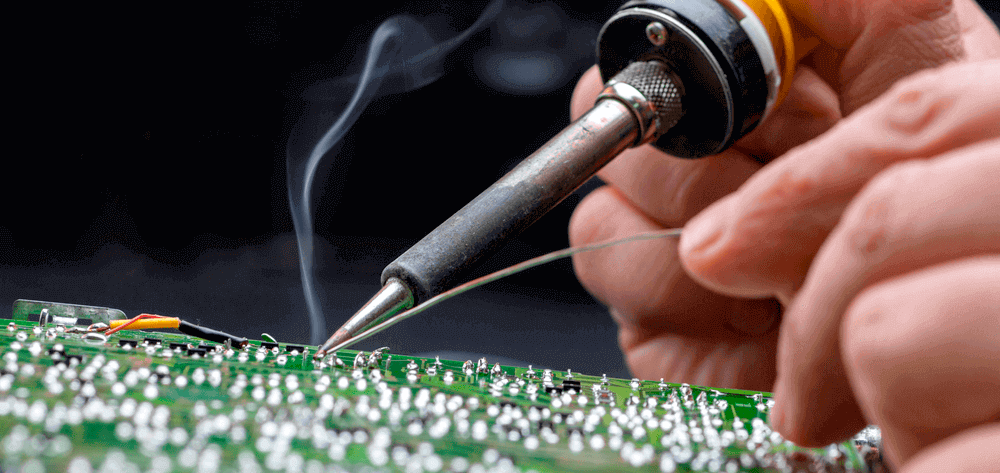
There are a bunch of solders used on a regular basis. Well, you’re not alone if you find yourself standing in a store, staring and thinking “there just so many of them, so, what do I choose”? The fact is a lot of people get confused with this because there really is a wide range of what to use and many people make common mistakes when trying to find the best solder for electronics. There are basic things anyone looking to use it should be aware of. First off, what is solder and why is it used?
A solder is a material (an alloy, typically, tin, or lead) used to join soft metals, such as copper, gold, and silver. In solder for electronics, there is mostly lead and tin. For fixes or remodeling, you may need soldering. For example, models and vintage cars, soldering from radiators to batteries, allows you to bind metals together and at a lower temperature than would brazing or welding. Regardless of the use, one thing is for sure: you need solder flux.
However, you’ll have to know more than just what an electrical solder does in order to find one that fits your needs. While it is certainly a challenge to find the right tools, but it isn’t impossible. That is why I will point out the key differences between and how to use it.
P.S. In preparing this list, I tested literally dozens of products. But in rounding up the final, I had considered a number of factors including features of the products, value for money, and reputation of the manufacturer. Without further ado, let’s get started.
Solder for Electronics Reviews
Kester 24-6337-0027 – best solder flux for electronics
The Kester 24-6337-0010 possesses good conduction and control abilities. It also comes with a solid rosin core flux that’s adequately compatible with small electronics. Additionally, there’s a whopping 1-pound spool in-built in the solder. This Kester 63/37 wire is lead-based and has a small 0.31-inch diameter. The size makes it handy for small through-hole or larger surface-mounted components where lead solder will stick. It’s, however, a bit more difficult for use in filling in larger solder lugs on the vintage. The most relevant application for it may be on point-to-point wiring.
As with all soldering work, it’s important to remember that proper ventilation is required. But it appears to be more in this type of solder because the lead content is uncomfortable for breathing and will be in the smoke and fumes. Wear a mask while soldering with it in order not to breathe the fumes! Unfortunately, this has been the nature of lead-based solder and had been the standard. These days, there are newer printed circuit board materials that are optimized for both non-lead solder and lead-based soldering works. So, you can add a layer of protection with one of those. Vintage rework generally works better with the lead but will work with non-lead solder with the help of the RA type flux.
Pros
- Even though it’s more expensive than the rest, its effect is many times more potent. So, it’s really okay if you don’t mind paying a little extra for it that I’m sure won’t let you down.
- The included rosin makes it better than the core solder.
Cons
- Because of the excess of the flux in this solder, the iron-chrome plated tip begins to turn brown.
Canfield WBCANFIELD6040 – best solder wire for electronics
Since most glass artists need a very specific mix of alloys in their solder to get a smooth and clean bead on their work, Canfield is a good example to be used here. Any other type could be difficult and sometimes impossible to work with. Because it is the 60/40 (which means 60% tin and 40% lead), it stays in a liquid stage longer, giving you more time to produce smooth solder seams. It also melts at a lower temperature than 50/50 and is popular among beginners as well as experienced crafters. You should also know that it does quite well for use on copper foil seams and lead came seams. The average melting temperature is between 361° and 376°F.
Pros
- Offers superior flow when compared to some solders.
- Even melting.
Cons
- Pretty hard to work with.
Kester 24-6337-0010
The Kester Rosin is an activated rosin formula for use in flux-cored solder wire. The Rosin Core has virtually dominated the field of activated rosin core solders for well over four decades. It is leaded solder and otherwise called the fully activated Rosin core. The core in the name indicates a flux content that can be 1,2,3 – percent flux content. This is the easiest solder to work with. It has an instant welding action. The high mobility and fast-spreading action of this flux results in a more reliable production. The Kester is classified as ROM1 per J-STD-004 and can be the best solder for electronics.
Pros
- Good for SMD work.
- Works great at low temperatures.
Cons
- Too long solder keeps tangling.
Victory White Metal 60/40 – SG16
I tested many rolls of this solder a couple of months ago due to the good reviews I read on it, and I was very satisfied with both the quality and price. Normally, I used it for my stained glass (because my supplies were getting low). If you’re planning on getting one like this, you should probably add gloves to your budget. Using gloves prevents it from spilling on surfaces which is a good one considering the fact that it kind of saves you a little more for your next usage. Contrary to the 60/40 and 63/37, the Victory SG16 wire is metal-based (predominantly silver metal). It has plenty of flux so, don’t worry about not achieving a great window seal.
Pros
- Solid wire solder.
- Good for starters.
Cons
- Sometimes it also happens that it doesn’t attract the fluxed copper foil. It won’t flow properly nor will it bead well. Just makes you think as though there is no flux in it.
Maiyum
The product features good staying power and provides high-quality soldering of small electronic components. Its low-range melting point of 361°F prevents thermally sensitive components from damage and, at the same time, keep the previously joined areas safe. Besides, the unit is suitable for work with the materials that are sensitive to high temperatures or have different coefficients of thermal expansion. It is capable of double coating any joint, making even layers. Note that the solder is not compatible with stained glass and doesn’t suit to repair jewelry.
The solder contains 1.8% of rosin core flux in the wire’s core to clean and remove oxide from the surface, providing easy soldering with no flux residue. This item has no significant magnetic properties that allow soldering common electronic applications trouble-free and making strong joints. It’s crucial to not overheat the solder to avoid clumps.
Pros
- The flawless flowing of the rosin flux.
- A 50-gram spool is enough for a significant amount of projects.
- No unpleasant smell at all.
Cons
- The alloy contains lead that is not good for health and the environment. So, it’s not recommended for soldering all day long.
- The unit is too thin (0.0314 inches) to solder wires and LED leads properly (0.039-inch solder is preferable).
Wyctin
Despite 40% of lead, making this product toxic, it might become the best solder iron for electronics. The item features a low melting point of 361°F and mild reactivity with no smoke. Its thickness of 0.236 inches makes it suitable for joining such tiny electronic elements as, for example, speaker wires, electric guitar components, or small circuit boards. The solder contains rosin; that’s why it is not compatible with stainless steel and nickel. However, it works well with copper, tin, silver, and copper-, silver-, and tin-plated elements.
The solder heats up and flows well, flawlessly adhering to everything without. It leaves just the slightest flux residue on the surface (use alcohol to remove it in a minute), and doesn’t spill all over the working area. The joints are neat, even, and feature no clumps. They seem to be durable and long-lasting.
Pros
- The solder is easy to use, as it melts in proper time, keeping a good consistency.
- A highly conductive product works well even with a very low voltage current.
Cons
- More flux in a solder would be great to avoid using extra tools to deoxidize the surface.
- The small diameter makes the unit suitable for a small range of DIY projects.
Alpha Fry AT-31604
The Alpha rosin core is an American made item and contains about 4 lbs of 1/16. It is also a lead-based model of 60/40. This solder seems to flow so well and when I used it on track or circuit boards, it did the job so much better than the previous solders I have mentioned. It’s melting point is 376 degrees Fahrenheit. It is around 1.1mm thick. I need to mention that it’s not sold in length but rather in weight. From the name, you already know it has a rosin core and shouldn’t need additional flux.
Pros
- It doesn’t give off that acidic effect (aggressive).
Cons
- It’s a bit too thick for smaller electronics.
Buyer’s Guide
What is Solder Made of?
You should know that three key solder contents are lead, tin, and flux. Lead and tin improve the conductivity of it and retain its liquid state respectively. The main needs of flux, on the other hand, may be put into various parts. It forms an effective spread across the soldering. Then, it keeps the metal clean until the solder alloy reaches its path. Finally, it increases how much of the solder spreads on the metal surface. Put simply, flux could be considered an aqueous solution and is made up of a solvent, activator, and wetting agent. Below are examples of what it could be made from:
- Copper blend. It decreases the melting point and improves the wetting properties.
- Antimony blend. It hypes the mechanical ability of Sn and at the same time stops additives from filtering into the solder (without cutting the weight resistance).
- Nickel blend. It acts as a shield for specific surfaces like UBM from damaging the soldering blend.
- Bismuth blend. It reduces the melting point significantly and improves weight resistance. It prevents whiskers from growing on the tin.
- Indium blend. It increases the melting point. Due to its high-temperature tolerance, ductility increases and is used in gold-plated or cryogenic applications. It’s also very pricey and quickly damages due to oxidation.
- Silver blend. It offers lower ductility than lead, however, it showcases great mechanical strength. It can boost thermal fatigue tolerance in lead-free solders.
While these metals can be of enormous advantages, depending on where you use them, there are a few things to be mindful of:
- Do not place metals of different groups with one another. This could lead to galvanic corrosion.
- If you have to combine metals, make sure you do so in specific conditions. Making a blend – 63% tin and 37% lead is most effective at 361 degrees Fahrenheit.
Soldering Electronics
Before we go into learning how to solder electronics, let’s first talk about things not to do (safety measures) and must-haves (tools).
- Putting solder on the iron first and then trying to carry it over to the stand in order to scrape it off.
- Applying solder on the iron and not directly on the spot to be soldered. Even if you get the solder to stick to the connection, it will likely be an unreliable join that will break with any vibration or temperature changes. The reason is that it won’t adhere to parts that aren’t hot enough or parts that are covered with dirt or oxidation (rust). Unfortunately, all metals oxidize and much faster at higher temperatures, this is problematic since soldering occurs at higher temperatures and solder won’t adhere to oxides the solution something like flux. After it removes oxides, flux acts as a placeholder to keep oxygen away until the solder displaces it. It also reduces the surface tension of solder to help it spread and acts as a blanket to help distribute heat.
Fast forward to how you can solder electronics. Let’s say you’ve purchased a brand new soldering iron. What’s the very first thing you should do before you even turn the soldering iron on?
Tools
- A soldering iron
- Rosin iron core
- A stand
- A sponge
For a soldering iron, it’s better to use one of 20-40 Watts. The higher the electric current, the faster it joins. However, higher, in this case, doesn’t mean hotter. Then as for the rosin core, ensure that its ration to the solder iron 1.0mm to 0.75mm. Next is a stand, and there are a lot of varieties you can choose from. And finally, use a damp sponge to wipe the solder iron’s tip.
Preparations
- Get some solder ready – whether it’s 63/37, 60/40, or lead-free, whatever you’re comfortable using, you need to have that ready.
- Put the soldering iron in a stand and do not turn it on until you have the solder ready. If the tip of your new solder remains dry, then it’s still not set right.
- Set the soldering iron between 572 or 662 degrees Fahrenheit. That’s a comfortable range to work with.
- Wet the sponge.
- Get your abrasive cleaner ready.
Step process
- Solder will stick to only a clean surface.
- Until soldering, dust the copper foil with steel wool.
- Remove all forms of oil or paint, wax, with solvent or wool or fine sandpaper, or any whatever you can access that point.
- Steam the solder for a few seconds, then add it to steam the contact to the tip of the metal.
- Heat up only the connection. You must avoid heating the solder.
- Hold the iron soldering near the bottom of the handle, just like a pen.
- If you want to form a good connection, then ensure that all parts that are soldered dry up first.
Types
Nowadays, the market offers various types of solder that it can be terrifying to choose the right one for repairs. Luckily, there are three main groups of solder classes to help you shorten the chase. Let’s take a look below.
- Lead group. The solders focused on lead basically changed the way people went about fixing electronics. A 60-40 (Sn/Pb) mixture with a melting point between 356-374°F happens to be the most frequently used solder blends. Tin has a relatively lower melting point than lead (this helps in making a liquid solder for electronics). Lead differently helps inhibit tin whiskers (tiny projections) from forming. With a higher concentration of the tin, concentration comes greater tenseness and mechanical strength.
- Nonlead group. The European Union passed a law to limit the content of lead in electronics widely used by consumers (this was a move to cut down lead poisoning that was fast becoming an epidemic). In fact, not only did some countries uphold the law, they also went as far as rewards manufacturers who were based on lead-free electronics. For instance, the US could provide tax benefits to manufacturers for using solders completely free of lead. The use of modern techniques like including additives (nickel) could also reduce tin whiskers. Lastly, non-lead solders have higher melting points than traditional ones.
- Flux group. This solder type is marketed as a “wire”, a substance at its core that reduces metals. In other words, a counter attacks the oxidation of metals. The flux is let out while soldering to solidify the wires being connected. The flux core is normally rosin and is used in electronics. The acid core is more for repairing metals or plumbing.
Another classification of solders is by their core type. There are two groups here.
- Acid-core. This type of wire is shaped like a wire, but its core contains acid flow. The acid center is more potent and corrosive than a cleaning flux. The use of this solder helps eliminate metal oxides and keep them from forming a strong link to it.
- Rosin core. The flux used is a smaller rosin variety which is of a solid shape and made out of conifer, like pine. It’s likewise produced with a hollow center fixed inside a wire.