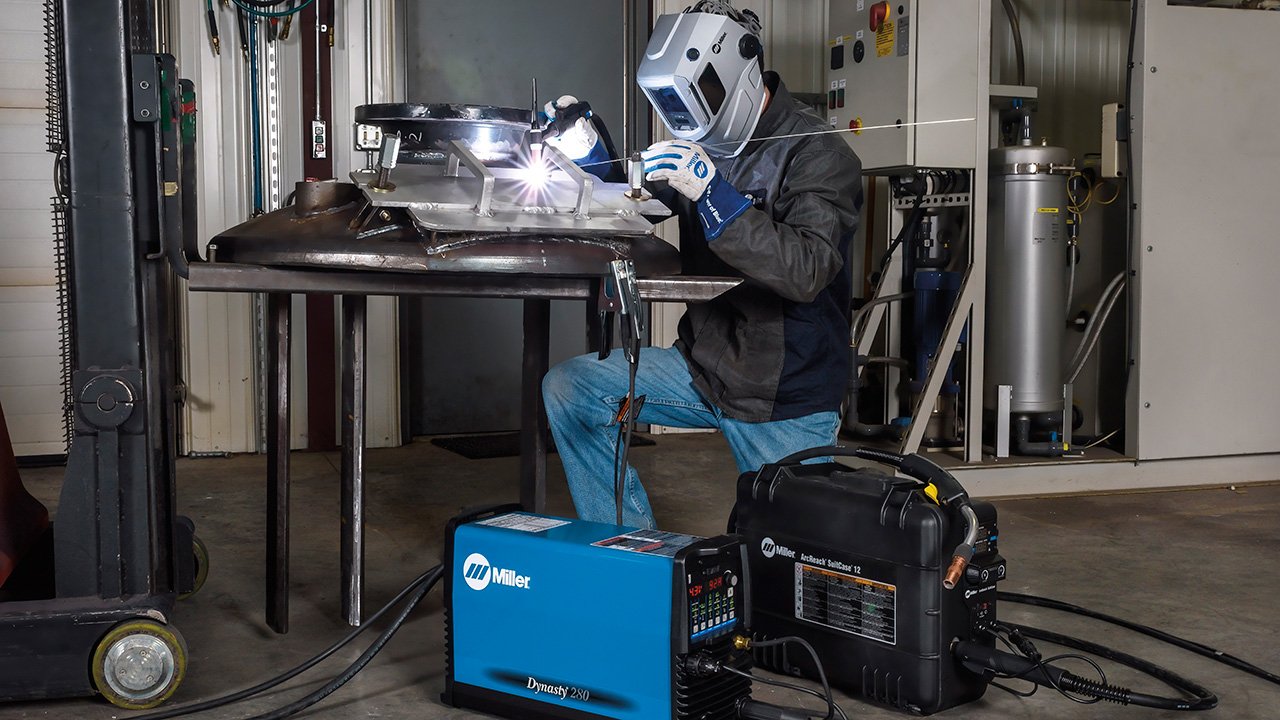
Arc welding – the process of fusion of materials, in which the heating is carried out by an electric arc. The temperature of the electric arc (to 7000 ° C) exceeds the melting point of all existing metals.
By the degree of mechanization distinguish the following types of arc welding:
- manual (MMA -Manual Metal Arc), in which the operations necessary for the formation of a seam, are executed manually by a person without the use of mechanisms;
- mechanized (semi-automatic) (MIG / MAG -Metal Inert / Active Gas). The latter is performed by a molten electrode, with the automatic feeding of the electrode wire to the welding zone, and other operations of this process remain manual;
- an automatic arc, in which the operations for excitation of the arc, maintaining a certain length of the arc, moving the arc along the line of seam insertion are mechanized; at the same time, the welding mode (current, voltage, velocity of arc, etc.) is more stable, which ensures uniformity of the quality of the seam by its length, while at the same time, great accuracy is required in the preparation and assembly of the parts under welding.
About welding machines and aggregates, the types of arc welding correlate with the modes of welding.
By the properties of the welding, electrode distinguishes methods of welding: an electrode that melts and does not melt (carbon, graphite, and tungsten).
At present arc welding with coated electrodes, melting and non-melted electrodes in protective gases, as well as arc welding under flux, are widely used in various industries.
Welding is one of the main technological processes of modern production. It is difficult to imagine an industry in which welding technologies would not be used. In some industries, the share of welding works reaches 55–65% of the total production time. Modern requirements for product quality, dictated by international standards, can not affect the welding production. A significant part of the welding work falls on the production of critical structures and products, with very stringent requirements for the quality of welding work.
Let’s talk in more detail about welding methods, namely: TIG and MIG
TIG – Tungsten Inert Gas – manual arc welding with a non-consumable electrode in an inert protective gas. Since tungsten is most often used as a material for non-consumable electrodes, the abbreviation WIG (Wolfram Inert Gas) is used in the German-language literature; sometimes found the designation GTA (Gas Tungsten Arc). It can be carried out with manual or automatic feeding of filler wire or without it. Since the use of argon as a protective gas is most common, the name “argon-arc welding” was assigned to this method.
It should be noted, however, that such a name is not entirely correct, because, in TIG welding, helium, nitrogen or various gas mixtures can also be used as shielding gas, there is also a method of atomic-hydrogen welding, which is similar in its physical nature to TIG, In addition, welding using argon as a shielding gas can also be carried out using a melting electrode.
When describing TIG welding equipment, mentioning the welding method itself is usually complemented by mentioning the type of welding current: DC (Direct Current) – direct current – or AC / DC (Alternating Current / Direct Current). Let’s talk more about the best MIG welder for beginner, different types of welding, the difference between TIG and MIG welding.
TIG welding
TIG – manual welding with non-consumable tungsten electrodes in a protective gas – argon environment. The direct current TIG method (TIG-DC) is used for steels, the alternating current TIG method (TIG-AC) is used for aluminum alloys.
Pros of the TIG method
- Neat weld seam;
- Lack of spray;
- Welding parts of small thickness;
- Better control arc parameters.
Cons of the TIG method
- High requirements for operator experience;
- Low performance;
- The presence of a gas cylinder.
MIG / MAG – Metal Inert / Active Gas – arc welding with the consumable metal electrode (wire) in an inert/active protective gas environment with automatic feeding of filler wire. This semiautomatic shielded gas welding is the most versatile and widely used welding method in the industry. Sometimes this welding method is referred to as GMA (Gas Metal Arc).
The use of the term “semi-automatic” is not entirely correct, since it is a question of automating only the filing of the filler wire, and the MIG / MAG method itself is successfully used in automated and robotic welding.
The phrase “in carbon dioxide”, to which many specialists have become accustomed, has been deliberately omitted since this method increasingly uses multicomponent gas mixtures, which may include argon, oxygen, helium, nitrogen and other gases in addition to carbon dioxide.
MIG / MAG welding
MIG / MAG – semi-automatic welding with electrode wire in a protective gas medium – inert (argon) or active (carbon dioxide). It is used for welding steels (including stainless) and aluminum alloys. TIG or MIG welder? Each method has its advantages and disadvantages, each chooses what it needs.