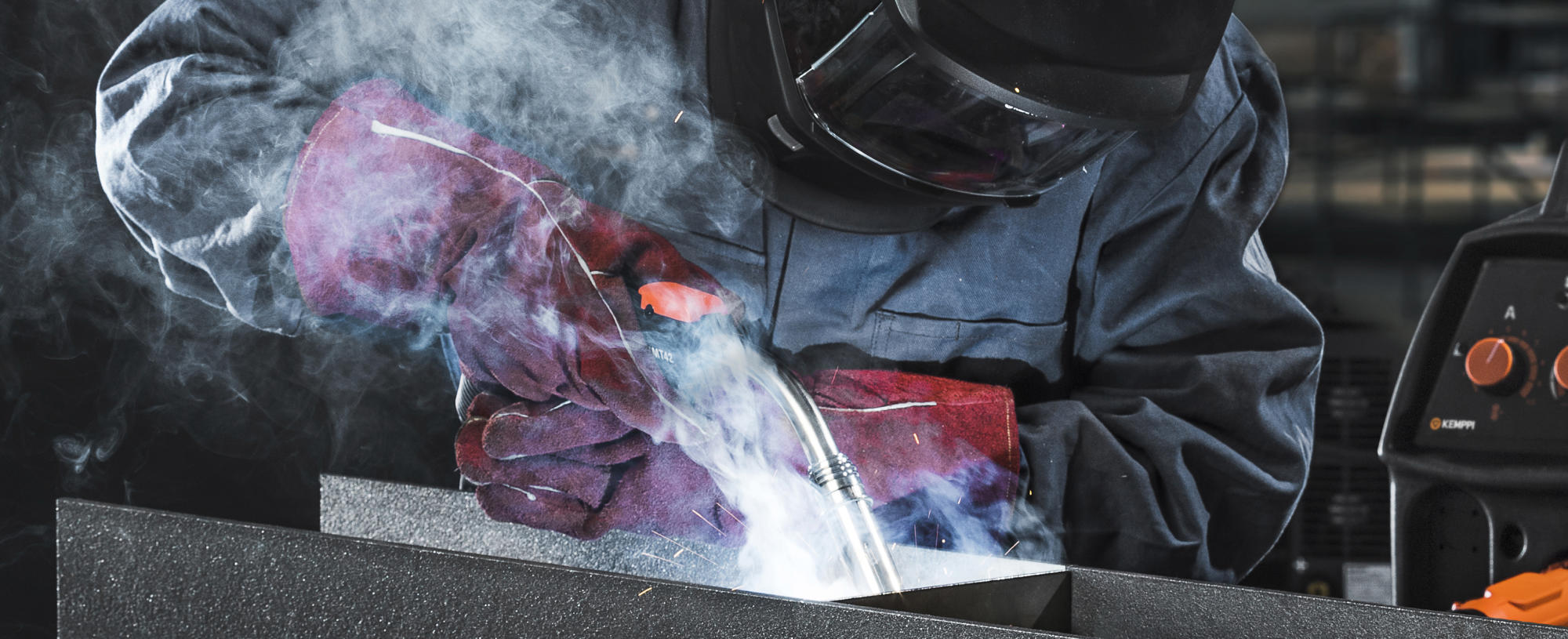
MIG welding involves welding with an electric arc produced between the consumable electrode and the welded material. The melting electrode is a continuous wire. The arc of the liquid metal is protected by the flow of protective gas. This topic touches on some important questions that people with no experience are interested in when looking for answers to these questions in Google: “best MIG welder for beginner“, “what is MIG welding”, “what does MIG welder stand for”, “MIG welding meaning”. Let’s consider them more in detail.
For the process of welding an expense electrode the following specific terms are used:
- MIG – (metal inert gas) – This name is used to describe the welding process when a chemically inert gas is used as a protective gas, such as argon, helium;
- MAG – (Metal Active Gas) – This name is used to describe the welding process when a chemically active gas, such as CO2, is used as a protective gas;
- GMAW – (Gas Metal Arc Welding) – The abbreviation used mainly in the US is common to both methods: MIG and MAG and indicates the use of solid wire;
- FCAW – (welding with arc elements) is an abbreviation for the method of welding, similar to the MIG / MAG (GMAW) method, with the difference that instead of solid wire, powder wire (powder) is used. If the wire is filled with a welding powder that produces welding gases (Innershield method), then it is not necessary to supply the gas from the outside (from the cylinder).
MIG welding is a common name for the welding process using the MIG method.
Welding MIG / MAG is currently the most widely used welding method, which covers about 65% of all methods of industrial arc welding.
MIG welding at a glance:
- The welding wire runs smoothly from the holder, which is constantly melted in an electric arc. The material of the molten wire is mixed with a molten bonding material to form a flowing weld bath. After the arc comes out, the welding bath stays cold, forming a constant layer. A protective gas is constantly fed through a welding gun and its gas nozzle, which protects the molten metal from the atmosphere and cools the handle (liquid-cooled handles are also used);
- (semiautomatic welding) and then transmitted by the copper current.
Features of using the MIG welding method.
Advantages of the MIG welding method:
- a universal method – you can weld various metals and their alloys in all positions;
- high efficiency of welding – much higher than coated electrodes;
- relatively low cost of welding materials – the total cost is lower by 20% than the cost of welding with coated electrodes;
- good quality welds;
- the ability to mechanize and automate the method.
Disadvantages of the MIG welding method:
- the quality of the weld depends largely on the skills of the person who welds;
- relatively high costs for the purchase of equipment for using this welding method;
- the method of MIG welding. Has a greater tendency to stick and porosity of welds.
Application of the MIG / MAG method
The MAG method is used to connect non-alloy structural steel, low-alloy and high-alloy structural steel, the MIG method is used to weld aluminum, magnesium, copper and other non-ferrous metals and their alloys.
Using the MIG method, welding is used in virtually all sectors of the welding industry, including the heavy machinery industry, including metal constructions, pipelines, various pressure vessels, and repair and maintenance services.
This method is widely used in the manufacturing of sheet metal, especially in automobile, bodywork and small industries. The MIG method is also often used for hobbies or homework.
MIG / MAG – Metal Inert / Active Gas – arc welding with an electrode melted by a metal electrode (wire) in an inert/active gas medium with an automatic supply of the adductor wire. This is semi-automatic welding in a protective gas environment – the most versatile and widespread in the industrial welding method. Sometimes this welding method denotes GMA (Gas Metal Arc). The use of the term “semi-automatic” is not entirely correct, since it is a question of automating only the supply of the connecting wire, and the MIG / MAG method is successfully used in automated and robotic welding. The phrase “in carbon dioxide”, to which many experts have become accustomed, is deliberately lost, since in this method more and more often used multicomponent gas mixtures, which in addition to carbon dioxide can include argon, oxygen, helium, nitrogen and other gases.
Depending on the metal being welded and its thickness, inert, active gases, or mixtures thereof are used as protective gases. Due to physical features, the stability of the arc and its technological properties are higher when using a DC reverse polarity. When using direct-current direct polarity, the amount of molten electrode metal increases by 25 … 30%, but sharply decreases the stability of the arc and increases the loss of metal spray. The use of alternating current is impossible due to the unstable burning of the arc.
When welding, the melting seam is formed by the melting of the base metal and melting of the additional metal – electrode wire. Therefore, the shape and dimensions of the seam, among other things (welding speed, the spatial position of the electrode and products, etc.) also depend on the nature of melting and the transfer of electrode metal into a weld bath. The nature of the transfer of the electrode metal is determined mainly by the material of the electrode, the composition of the protective gas, the density of the welding current and several other factors.
In the traditional method of welding, three basic forms of electrode melting and the transfer of electrode metal to a weld bath can be distinguished.